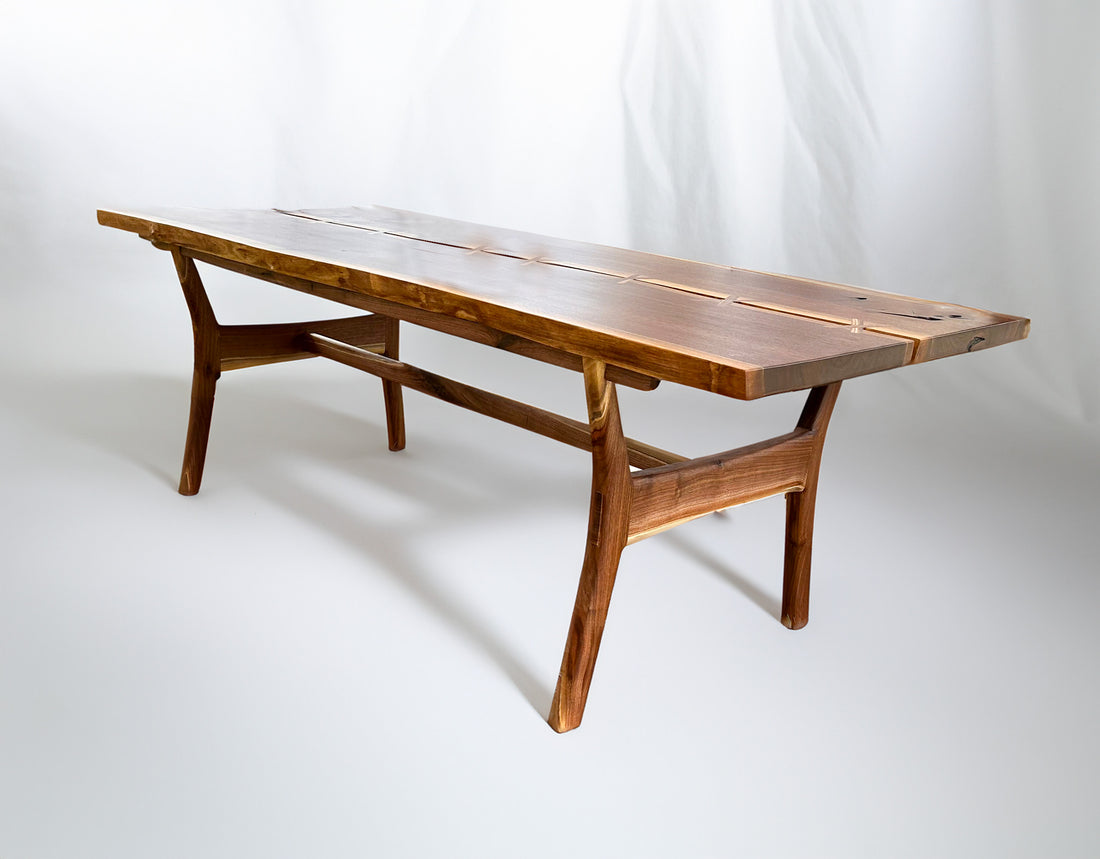
Understanding Wood Movement: Designing for Durability and Beauty
Understanding Wood Movement: Designing for Durability and Beauty
Wood is a beautiful and versatile material, but it has a unique characteristic that every woodworker must respect: it moves. Unlike synthetic materials, wood is hygroscopic, meaning it absorbs and releases moisture from the air, causing it to expand and contract with changes in humidity. This natural movement can present challenges in furniture design and construction, but with careful planning and expertise, we can create durable and aesthetically pleasing pieces.
The Science Behind Wood Movement
Wood movement occurs primarily across the grain, with minimal movement along the grain. This natural movement, known as wood's dimensional change coefficient, varies with the species but generally ranges from 0.1% to 0.3% for every 1% change in moisture content. For example, a 12-inch-wide piece of oak will shrink or expand by around 3/32 of an inch with a 6% change in moisture content. Movement occurs primarily across the grain, with minimal changes along the grain. The extent of this movement depends on the wood species, how it was cut, and the environmental conditions it lives in.
Take my recent, “Stitch Table,” dining table for example. This top consists of two quarter-sawn slabs of walnut with a combined width of roughly 40 inches. We can do some quick math to determine the expected dimensional changes. We'll assume an average change in moisture content of 6% from the highest to the lowest humidity levels. Quarter-sawn walnut has a dimensional change coefficient (shrinkage rate) of approximately 0.0015 per 1% change in moisture content. This means the change in width will be ±0.36 inches, resulting in a maximum width of 40.36 inches in the most humid parts of summer and a minimum width of 39.64 inches in the less humid months of winter. When I designed the mounting mechanism for this top, I couldn’t just glue it to the base or firmly attach it without allowing for any movement, as some factory furniture manufacturers do. I have to:
Designing to Accommodate Wood Movement
At Fahr Fine Furnishing, I embrace the challenge of wood movement by designing my pieces with this natural phenomenon in mind. Here are some of the strategies I use to ensure that my furniture can handle wood movement gracefully:
1. Floating Panels
One of the most common methods to accommodate wood movement is by using floating panels in doors and tabletops. These panels are not glued to the frame; instead, they fit into grooves or are bolted to movable mounting mechanisms that allow them to expand and contract without causing stress to the surrounding structure. This technique maintains the structural integrity and aesthetic appeal of the piece. For my “Stitch Table,” I employed this technique, allowing the top to “float” on the base in a series of rotatable mounts. While the top is still firmly bolted to the base, it can expand and contract freely without causing undue stress on the base.
2. Breadboard Ends
Another feature you will see in well-designed furniture, typically when a top is glued up of multiple boards, is breadboard ends. A properly executed breadboard end is used on tabletops and wide panels to keep them flat while allowing for wood movement. The ends are attached with tenons that fit into mortises on the panel, secured with pins or screws in elongated holes. This construction allows the panel to expand and contract while keeping it aligned and stable. Unfortunately, most of the time, these are done incorrectly, serving more as an aesthetic feature than a functional support, causing more problems than they solve.
3. Strategic Joinery
I carefully select and implement joinery techniques that can handle movement. For example, I use dovetail joints for their strength and ability to accommodate wood movement. In table bases, I use a lot of mortise and tenon joinery for its ability to get stronger as the wood expands in its mortises. In frame and panel construction, the frame is designed to hold the panel securely while allowing it to move freely.
4. Proper Material Selection
Choosing the right wood species and grain orientation is crucial. I prefer quarter-sawn or rift-sawn lumber for its dimensional stability compared to plain-sawn wood. These cuts reduce the amount of seasonal movement, making them ideal for fine furniture. When combining multiple species into a single piece, I must be particularly cognizant of the individual movement coefficients and make sure to allow each species its required space to breathe.
5. Environmental Control
Maintaining a consistent environment in my workshop and advising my customers on proper humidity levels helps minimize drastic changes in wood movement. I recommend keeping furniture in an environment with stable humidity to prolong its life and maintain its beauty. However, I know this isn’t always possible, and a piece built in my workshop in Connecticut, sent to a home in Boulder, CO, or Ireland, will immediately be shocked into acclimatization in its new home, making the proper implementation of design even more critical to the longevity of the piece.
The Art of Balancing Form and Function
My goal is to create furniture that not only looks stunning but also stands the test of time. By understanding and respecting wood movement, I can design pieces that adapt to their environment without compromising their structural integrity. Each piece from Fahr Fine Furnishing is a testament to my commitment to quality craftsmanship and a deep appreciation for the natural beauty of wood.
Conclusion
Wood movement is an inherent part of working with this wonderful material. At Fahr Fine Furnishing, I take pride in my ability to design and construct furniture that accommodates these natural changes. Through thoughtful design and expert craftsmanship, I create pieces that are as durable as they are beautiful. Whether you’re looking for a custom dining table, a unique cabinet, or a timeless piece of decor, you can trust that my furniture is built to last.
Thank you for joining me on this journey into the heart of woodworking. Stay tuned for more insights and tips on caring for your fine furnishings!